It shouldn’t surprise anyone to hear that fired brick (made from clay or shale) doesn’t burn. Bricks are not made of combustible material and they are typically fired to temperatures around 2,000 degrees Fahrenheit to make them. If they were combustible, they would come out of the manufacturing process as a pile of ash – which, of course, they don’t. Interstate Brick makes a color called Ash, but that is just the name of the light gray color, not a description of the material!
Before we delve further into fire resiliency of masonry it is worth noting that some manufacturers make brick specifically for high temperature environments like fireplaces, brick ovens, and other normally high-temperature uses. A couple of those standards for brick used in high temperature environments are ASTM C27 Standard Classification of Fireclay and High-Alumina Refractory Brick, and C1261 Standard Specification for Firebox Brick for Residential Fireplaces. There are other standards for brick used in industrial flues and chimneys. This article is not about those particular applications. This article is about the typical modern fired clay brick for face brick (ASTM C216) or building brick (ASTM C62) used for veneers, and about hollow clay masonry (ASTM C652) used in structural reinforced applications, and thin brick (ASTM C1088) used for light weight adhered applications.
From October 8 through October 10, 1871, most of Chicago was on fire (the city was much smaller then, than it is now). The Great Chicago Fire, to which it became known, consumed, or damaged more than 17,500 buildings, over an area larger than 2,000 acres, (some say 4-square miles) leaving roughly one-third of the residents homeless. Chicago burned to the extent it did because the principal building material was wood, and the police and fire responders were not well trained for this large of a catastrophe. Further complications arose when the city’s waterworks building caught fire and was destroyed, causing the water mains to go dry. The palatial Palmer House Hotel burned to the ground only 13 days after its grand opening due to the Great Chicago Fire. Many people were never able to fully bounce back from the disaster as their personal papers (birth certificates, deeds of ownership, licenses, and registrations papers) were consumed in the catastrophic inferno.
One of the more outspoken landscape architects and social critics of the time, Frederick L. Olmstead, believed that had buildings been built with brick (a readily available building material), and a better disciplined emergency response system (firemen and police) had been in place, the loss of life and damage would have been much less. Almost immediately after the fire the city began to rewrite its fire [resistive] standards.
After the fire, laws were passed to prevent the same kind of calamity from happening again. Wood construction was banned from the downtown area. Masonry, which included brick, became the preferred and predominant building material in Chicago, and changed the architectural appearance of the city.
Of particular note are two buildings that were built in accordance with the updated provisions after the fire. The re-built Palmer House Hotel, “built with brick and iron”, opened on November 8, 1873, and was marketed as the “World’s First Fireproof Building”. It remains the longest continually operating hotel in the United States of America – 150 years and counting. The other building is the Monadnock Building (Figure No. 1), built in 1891 and doubled in size in 1893 which is still the tallest load-bearing brick building in the world, at 16 stories and 215 feet high. It was the largest office building in the world when it was fully completed. The Monadnock still stands as the sentinel of the business center of the city that arose at the southern end of the Loop in Chicago – 132 years and counting.
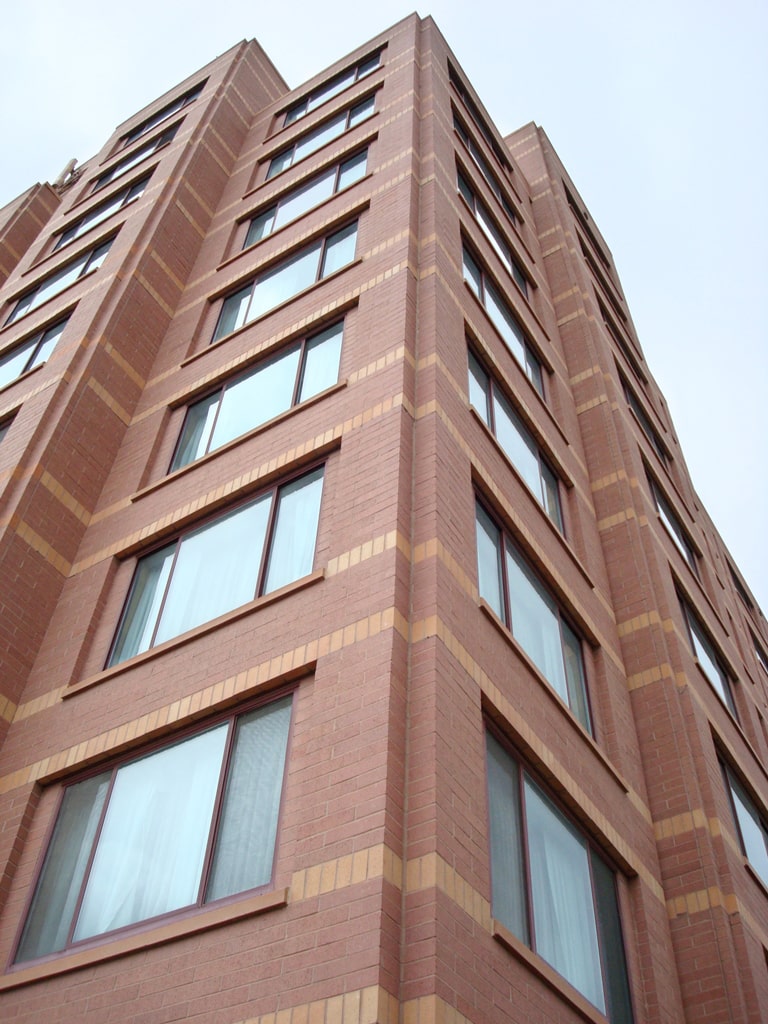
These are but a couple of examples in one city of many examples in many cities of the benefits of brick construction combined with other non-combustible materials that enhance resiliency for individuals, families, neighborhoods, communities, and beyond.
Durability and resiliency equate to longevity– standing the test of time. Structures that are built to last with durable materials enhance resiliency. If it doesn’t burn down, nor isn’t damaged by fire, then re-occupancy occurs more rapidly, possessions are not lost, and resiliency is improved.
One can easily understand that an apartment building (or hotel), for instance, built with structural masonry load bearing walls, structural masonry shear walls, structural masonry stair walls, and structural masonry dividing walls combined with any number of concrete or steel and concrete floor and roof systems will perform significantly better in a fire situation as compared to a wood framed building. The durability of such a structure is extremely high; the potential of structural damage is relatively low. This high durability enhances resiliency of the occupant or occupants. In the aforementioned apartment building assumed to be constructed of structural masonry, concrete, and steel, if a fire starts in one apartment, it is likely to remain contained in that one room, or one domicile, and is unlikely to spread to adjacent units. The masonry construction provides 100% passive fire resistance 100% of the time. Nothing to monitor, test, check, or actively manage.
The NFPA published a study from 2010 titled “U.S. EXPERIENCE WITH SPRINKLERS AND OTHER AUTOMATIC FIRE EXTINGUISHING EQUIPMENT” by John R. Hall, Jr. of actively sprinklered buildings. Based on that study, it was found that the active fire suppression sprinkler system was only activated 93% of the time, and of those times that it operated, it was only responsible for suppressing the fire to a discernible level 97% of the time. That means active suppression systems were only effective in suppressing a fire 91% of the time. Non-combustible materials, like masonry and concrete, are 100% effective, 100% of the time.
The current (2021) International Building Code, as have past IBC and UBC codes, includes a table that defines the fire-resistive ratings for concrete masonry walls (Table 722.3.2; Figure No. 2)
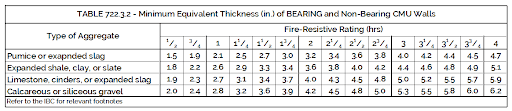
A similar fire-resistive ratings table exists for clay brick walls (Table 722.4.1(1); Figure No. 3), based on the type or profile of the clay brick material being used.
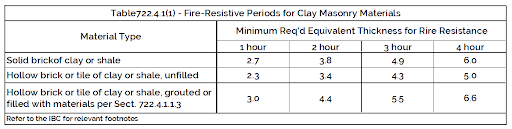
It is worth noting that for a wall to receive a fire-resistive rating it must perform in resisting the heat buildup from both directions, in other words, from both sides of the wall, unless specified otherwise. Therefore, the fire-resistive ratings from the aforementioned Table 722.4.1(1) using brick veneer (top row – “Solid brick of clay or shale”) are for one side only of a brick veneer wall. The opposite face of a brick veneer wall will frequently require one or more layers of Type X fire rated gypsum board for any specific fire-resistive rating. Particulars of face brick wall assemblies can be found in Table 721.1(2) for listed times 15-2.3 and 15-2.4, for 1-hour and 2-our rated walls, respectively.
For typical 3-5/8” deep brick facing material that has up to 25% voids in the bedding plane (allowed by ASTM C216) will attain a fire-resistive rating of 1-hour, based on an equivalent solid thickness of 2.71 inches [3.625” x 0.75 solid = 2.71” inches equivalent solid thickness; which is greater than 2.7” as per the table in the 1- hour column for solid brick]. King size brick with 25% void does not meet the minimum equivalent solid thickness due to the 3” bed depth. For King size brick to meet the 1-hour rating, the void percentage would need to be reduced to 10%. [3” x 0.90 = 2.7”].

For hollow clay structural masonry units there are two options: unfilled and grouted or filled. Because a partially grouted wall may have areas, perhaps significant areas, that are ungrouted, the entire wall is considered unfilled for purposes of determining the fire resistive rating. A grouted wall is assumed to be filled with ASTM C476 compliant cementitious masonry grout and reinforcing. A “filled” wall may be filled with any number of materials, as follows: sand, pea gravel, crushed stone, slag that meet ASTM C33 requirements; pumice, scoria, expanded shale, expanded clay, expanded slate, expanded slag, expanded fly ash, cinders in compliance with ASTM C331; or perlite or vermiculite meeting the requirements of ASTM C549 and ASTM C516, respectively
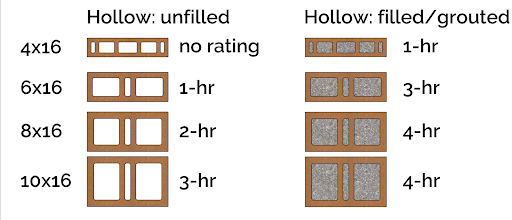
There is also a fire-resistive table in the IBC that addresses thin brick applications – thin brick applied over cement plaster (stucco). The table indicates that if the finish system assembly (thin brick + setting bed mortar + cement plaster and lath backing is a minimum of 1.75” thick and the wall assembly includes one layer of Type X gypsum board on the inside face of the wall, the assembly will receive a 1-hour fire-resistive rating. If the assembly is thickened to a minimum of 2” for the thin brick + setting mortar + cement plaster and lath, and a second layer of Type X gypsum board is applied to the inside of the wall, a 2-hour fire-resistive rating can be achieved. Additional particulars for these assemblies (stud size, spacing, fasteners, etc.) can be found in Table 721.1(2) for listed times, numbers 15-2.1 and 15-2.2, for the 1-hour and 2-hour rated walls, respectively.
Fire can be a destructive force that can cause injury and loss of life as well as extensive physical damage to personal and public property including homes and businesses, roads and bridges, and various infrastructure facilities. Fire can change one’s life trajectory if certain important documents and records are permanently lost or if unrecoverable injuries are incurred.
The example of the pre-1891 Chicago Waterworks Building noted earlier is a prime example of why some – or all – essential facilities should (must) be built to a higher fire resistive standard. This higher fire-resistive standard can easily incorporate masonry as one of the few systems that can effectively resist fire 100% of the time in a passive, non-obtrusive way.
It has been shown that there are a number of assemblies using brick veneer, thin brick, and single wythe structural masonry (brick and block) that can achieve various fire-resistive ratings, as high as 4-hours in the case of 8” and 10” deep grouted or filled structural masonry units. These options can and will provide many solutions for situations where fire-resistive ratings are mandated.